LDC (Lighting Design Collective), Silo 468 (2012). Helsinki (Finlande)
| Finlande / Finland (Helsinki) |
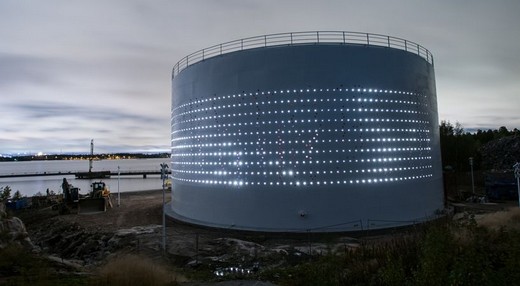 © Lighting Design Collective
Photo : 1 2 3 4 5 6 ‘When we were installing it one of the client team asked if they could touch it. Concrete isn’t known for its tactile qualities. Maybe that’s a first! ‘Crushedwall is, for me, about two things. It’s about geology. And it’s about process, the way that things are made.’ ‘Geology first. Heartlands sits over a very special geology. 19th century miners dug an astonishing 1000 metres down through granite to extract tin ore. This is one of the hidden stories that Heartlands will celebrate. When we were asked to design a retaining–wall the geological connection seemed serendipitious. Retaining walls hold back the geology. They are the boundary between our above-ground world and the world of mining. ‘And process. One of the things that interests me as a maker is the way in which made things are so much duller than the processes that got them there. Watch glass blowing and you’ll see more beauty there than you’ll ever see in the finished vase! Concrete is not noted for its fluid softness. And yet it is a liquid. We wanted our concrete to tell its own story – to retain the liquidness of its process. ‘We started with a sheet of rubber, some plywood and a hired cement mixer in my back garden – and went from there. The final shutter was built in one piece – using a single sheet of rubber 40m long and 4 metres high – a tonne of rubber sheet. The wall needed more height at one end – so the rubber pretty much hangs like a curtain at that end. At the lower end 4 metres of rubber is crumpled down to 1.5 metres. The wall seems to change in mood – as well as shape. It become much stormier at the low end! ‘Once the shape was formed the shutter was carefully cut into six pieces. One of the challenges was to retain continuity of the fluid form between shutters. The 6 shutters (made by Richard Stump and John Hall) were then taken from the barn in Gloucestershire where they were made to Ladd’s Concrete – only half a mile from the site. We’d done prototypes – but at this point we still didn’t really know whether the plan would work on this scale. The parts, weighing up to 20 tonnes each, were cast offsite and installed with millimetre accuracy – again to ensure continuity of form. http://www.ldcol.com http://vimeo.com/51983529 |